Buenaaass taringueros...es mi primer post, así que quería arrancar con esto...
siempre Fui fanático de los cuchillos, me han regalado varios...pero el acero con el que los hacen es malisimo y se desafilan de la nada.
Una mañana, estaba al re pedo en el trabajo (trabajo en una metalúrgica) y se me ocurrió fabricar mi propio cuchillo sin gastar mucha guita, entonces me fui hasta una chacarita que conozco y busque un pedazo de acero elástico (esas tiras de acero que están abajo de los autos con forma arqueada)...bueno, el asunto es que encontre una tirada entre todo el quilombo y el chabon que estaba ahí prácticamente me la regalo(le di 20 mangos para una coca, tampoco soy tan judío)...de la tira de acero corte un pedazo de 15 cm aprox:
y arranque con la ardua tarea de empezar a gastarlo con una amoladora de mano.
Bueno después de que me quedaran las orejas como si hubiese estado 2 días seguidos escuchando tan bionica termine de darle forma y afinarla :
con la idea de hacer el trabajo rápido le re di rosca con la amoladora, y el acero se calentó tanto que al parecer perdió un toque el temple, pero no me importo tanto, al contrario..eso me facilito las cosas para poder trabajarlo.
Desde el arranque quise evitar hacerle el típico mango con dos cachas de madera remachadas, asi que mi idea era la de un tubo de madera con un alma de acero roscada en la punta.
Entonces me puse a buscar un pedazo de acero groso para fabricar el alma del mango y encontré un vástago de cilindro hidráulico:
recorte un pedazo de 10 cm, para poder comenzar a torearlo ya que el diámetro del vástago es de 25 mm y yo necesitaba dejarlo de 11 mm aprox
una vez dado el diametro tenia que pensar que rosca le iba a hacer, por suerte se me prendió la lampara y para ahorrar tiempo, preferí tornearle la cabeza a un bulon de 7/16 (11 mm):
después de eso solo tuve que unir las dos cosas, que queden bien derechas y soldarlas:
después lo subí al torno y le di forma cilíndrica al cordón de soldadura para que entrara en el mango...
Â
una vez solucionado el asunto del alma del mango, empece a pensar como iba a apretar todo, necesitaba algo practico pero lindo...entonces me acorde que tenia pedazos de bronce tirados por ahí. El bronce es fácil de trabajar, es un metal bastante resistente y resiste bastante el oxido sumado a que si lo pulís bien queda genial. Entonces agarre un cuchillo que fabrique hace 5 años con la carcasa de un ruleman...pero sinceramente era mas blando que la defensa de brasil en el mundial, así que tenia que sacrificar el mango que le supe hacer, que era de puro bronce y mas pesado que novia indispuestaÂ
primero corte un pedacito de 25 mm de ancho por 40 mm de largo (que iba a ser la tuerca que apretara desde atrás al mango)...a este pedazo le hice un agujero de 9,5 mm y le pase un macho de "7/16 W " (el paso de la rosca que tenia el tornillo que le había soldado al alma)
despues, corte el otro pedazo que iba a necesitar...este pedazo de bronce tenia 18 mm de ancho y 60 de largo (es sobre el que apoya la hoja del cuchillo) a este pedazo le hice solamente un agujero de 11 mm, este no va roscado porque el alma pasa derecho:
despues de tener los dos pedazos cortados, tenia que dejarlos mas presentables y como no tengo pulidora, tuve que poner la tela esmeril o lija, como quieran decirle, sobre una superficie plana y deslizar los pedazos de bronce sobre ella UN MONTÃ?N DE VECES,posta, me quedo el brazo como hell-boy, pero valió la pena, quedaron brillantes :
después, agarre el alma del mango y le di una forma redondeada en la punta...parecida a la de la muesca que le hice a la hoja del cuchillo, para poder soldar las dos cosas:
una vez soldado eso había algo que me preocupaba y era el temple de la hoja...como les dije antes después de darle tanta rosca con la amoladora y ahora con la soldadura, el acero había perdido la dureza que es justamente lo que hace tan grosos a los cuchillos de acero elástico...entonces mi viejo que es un GROSO laburando el acero me ayudo y le dio un temple ZARPADO (y esa es una de las cosas por las que le tengo tanto cariño a este cuchillo, tiene en el temple, la firma de mi viejo)...bueno al momento en el que lo templábamos no le saque fotos porque tenia que manipular acero al rojo vivo, un soplete, pinzas y todo eso...no tenia tiempo de estar sacando fotos. Pero lo que hizo es calentar la hoja a una temperatura altisima (quedo de color naranja oscuro) y sumergirla en aceite hidráulico, después de eso le da otra recalentada mas leve para quitarle un poco de rigidez y se deja enfriar lentamente entre 4 ladrillos recubiertos por una manta de cuero, entonces la hoja quedo durisima pero no quedo frágil, se la re banca.
Ahora venia la parte que mas me emocionaba de esto, la madera. No sabia cual usar...pero tenia que ser una resistente...entonces recordé que en un deposito del taller había visto unos pedazos de madera tirados...cuando me puse a verlos estaban bastante maltratados por la humedad y recagados a palos...me dijeron que eran pedazos de durmientes de una vía de trenes, osea, imagínense los años que tenían esos pedazos de madera, las buenas noticias eran que si eran durmientes de vía de tren...seguramente eran de quebracho colorado, una de las maderas mas duras de argentina (justamente se llaman quebrachos porque le quebraban las hachas a los leñadores de lo dura que es la madera):
tome el pedazo mas chico que encontré y con una sierra sin fin corte un pedazo cuadrado bastante grande :
y automaticamente volamos al torno para empezar a darle maaaasaaa
 despues de quedar tapado en viruta de madera y de haberle dado la forma cilindrica...le pase por el centro una mecha de 11 mm...y quedo finalmente mi tubo de madera de 33 mm de diametro exterior
una vez torneado todo el pedazo de madera  excedente...y ensamblar todas las partes quedo algo mas o menos asi
entonces solo faltaba embellecerlo y darle forma a todo junto. Mas tranquilo en mi casa prepare las lijas, barniz, y un flapper...un flapper es un disco para la amoladora formado por lijas,...afina las superficies y las deja re pulidas..
Arranca la parte final del supercuchilloÂ
a la rosca de atrás (donde aprieta el pedazo de bronce roscado) le coloque algunas gotas de un sellador de rosca que impide que se aflojen...la unica forma de aflojarla, después de ponerle eso, seria calentándola a 250 grados:
con el flapper empece a darle una forma liza a los costados
use casi todas las graduaciones de lijas :100, 150,180, 220,320,400...la verdad que quedo muy muy pulido
el broche de oro fue el barniz...al haber quedado tan pulida la superficie..la capa de barniz quedo GE-NI-AL :
Bueno gente! eso fue todo...mostré mas o menos de manera resumida el proceso de creación de un cuchillo bien argento..el consejo..anímense a hacer ese tipo de cosas...uno aprende bastante y se da cuenta que tiene mas habilidad de la que uno creia...yo por ejemplo, estoy pensando en ir y clavárselos en el culo a mis ex-profesores del cole técnico al que iba...que me verdugueaban mal jajaja
saludos.
imágenes exclusivas de la primer victima del supercuchillo....una tira de costilla rebelde !
domingo, 12 de abril de 2015
Fabrique mi propio cuchillo y te lo muestro a vos, titan

Mi nombre es Christian y actualmente estudio Computacon e informatica, tengo este blog, porque me gustan el diseño y sobre webs, espero disfruten del contenido de sitio y pueden informarse todo lo que puedan. .
Relacionados
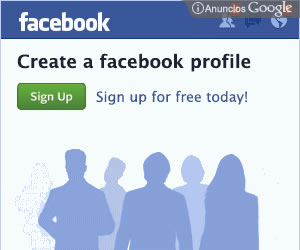
Suscribirse a:
Comentarios de la entrada (Atom)
0 comentarios
Publicar un comentario